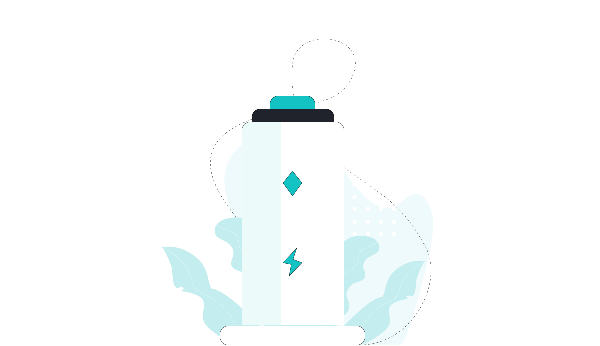
In the new energy battery production process, battery cell production is an important link. The back-end process of battery cell production includes formation, liquid injection, capacity division, liquid standing, and self-discharge testing, which are used to determine the battery's capacity, charging constant current ratio, discharge platform voltage, and internal resistance, so as to group batteries with the same characteristics. Battery's chemical composition and capacity is crucial to ensure the consistency, safety, and stability of the power battery pack. The traditional chemical composition process involves multiple charges and discharges. This process takes up to several days, consumes a lot of power and carbon emissions, seriously affects the improvement of power battery production capacity, and is accompanied by high process costs. The customer hopes to use the MengXi New Energy Intelligent Data Analysis System to realize digital low-capacity battery screening and capacity prediction, thereby optimizing the production line and increasing production capacity.
Compared with the traditional Battery's chemical composition and capacity method, the capacity dividing time is shortened by 80%, the energy consumption is reduced by 50%, the capacity dividing equipment is saved by 80%, and the equipment space is saved by 80%.
Daily prediction of 4000+ battery cells, cumulative prediction of battery 50W+
The normal predicted battery capacity remains above 70%, and the low-capacity battery screening rate is 99%
Use the capacity prediction results to group the cells into packs. It has been verified that the capacity differences within the cell groups are no more than 1%, and the internal resistance of the cells is controlled within 0.3mΩ, meeting the customer's factory requirements for group packs.
As of the statistical time, the battery packs currently grouped using the capacity prediction results have passed the customer's battery module verification test and met the factory requirements.